Amy Sprague
April 3, 2024
Jimmy O’Neil proves origami tubes deliver softer impacts and breaks a manufacturing barrier with broad applications.
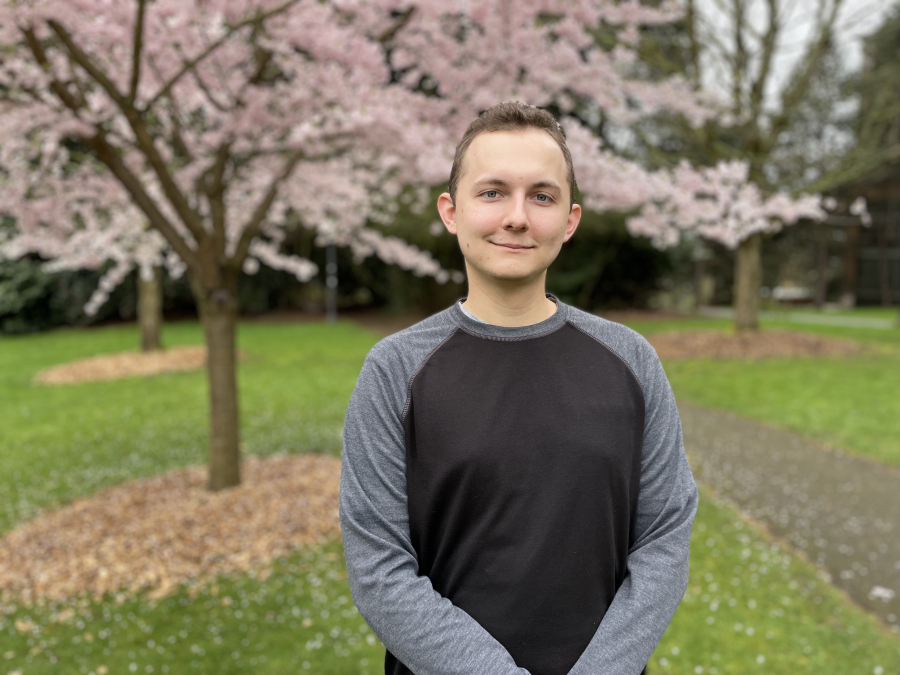
A&A Ph.D. student Jimmy O'Neil
A&A Ph.D. student Jimmy O'Neil has been awarded the Condit Fellowship in recognition of his groundbreaking research not only demonstrating that origami tubes can effectively deliver softer impacts, but also overcoming a significant manufacturing barrier that has wide-ranging applications across various industries.
Creases and folds can create safer structures
The curious notion of using creases and folds to make a safer structure intrigued Jimmy O’Neil early in his PhD career. Working in A&A’s Laboratory for Multiscale Analysis of Materials and Structures under associate professor Marco Salviato and co-advised by professor Jinkyu Yang, he is now a leading researcher of Kresling origami for crash resilience. For this research, he has been selected as this year’s A&A Condit Fellow.
Kresling origami fold pattern
The Kresling origami pattern is a foldable thin sheet of connected parallelograms through mountain crease lines. Each parallelogram is divided into two triangles by valley crease lines. When the ends of three or more parallelograms are attached, a Kresling unit cell is created. This origami pattern is known for its outstanding features, such as coupled axial compression and twisting during folding, deployability, bistable configurations, and rarefaction wave phenomena.
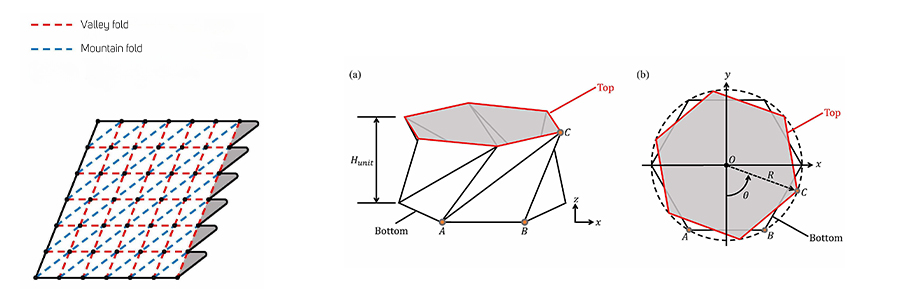
Kresling fold pattern and geometry.
Crash boxes, built into vehicles and aircraft, play a crucial role in redirecting kinetic energy from impacts by increasing collision time to reduce the forces transferred to passengers. But according to O’Neil, the limitations of modern-day crash boxes lie in their straight wall geometries, which, upon impact, “result in a high initial impact peak that is harsh for passengers.” O'Neil's research aims to overcome this challenge by introducing folds that combine compression with twisting in tubes, facilitating a smoother collapse during impact.
"My research utilizes a very particular origami architecture, known as Kresling, to facilitate a smoother collapse of a structure," O'Neil explained. By incorporating creases and folds, which act as geometric imperfections in straight walls, he has discovered a way to optimize the collapse of structures, reducing the intensity of impacts experienced by passengers.
Compression testing and results
O’Neil worked with five different shapes of tubes. He performed both slow and fast compression tests on each and measured the forces for each. The straight-walled cylinder and square showed the highest peak forces, with the three Kresling tubes having smaller peaks, confirming the potential for a smoother and safer experience for vehicles that might swap out straight-walled for Kresling tubes in crash boxes.
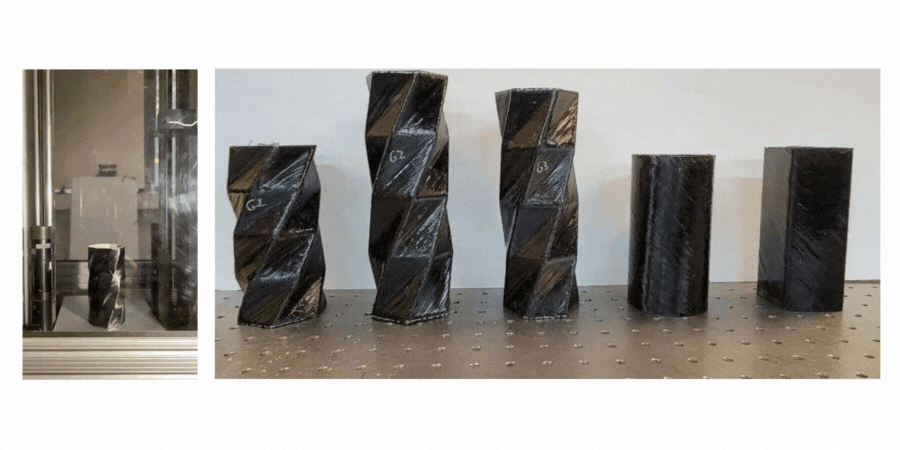
Left: A fast compression test on a Kresling origami tube. Right: O’Neil compressed five different test shapes to measure force and the smoothness of each shape’s collapse. From left: Three different iterations of Kresling origami (G1, G2, G3), a straight-walled cylinder and square tubes.
One of the slow compression tests on a Kresling origami tube.
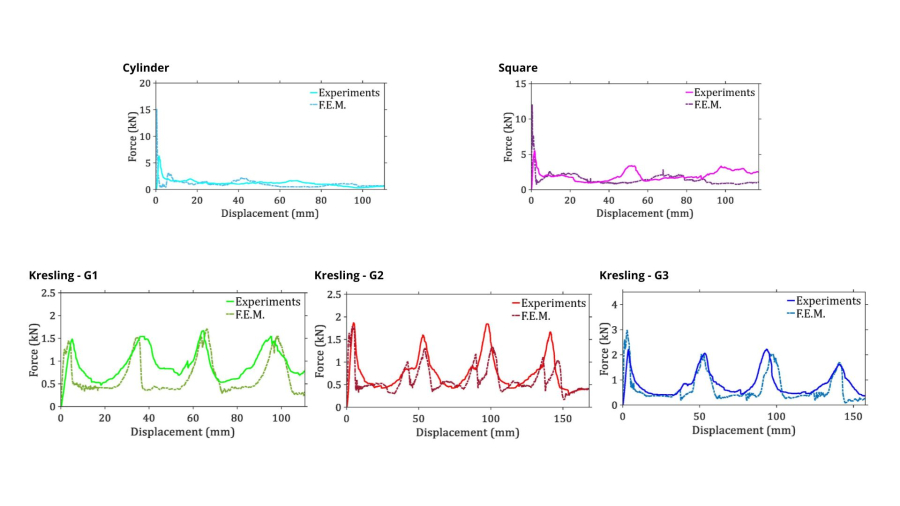
Test results show that the straight-walled tubes register far greater initial peak force (6.30kN for the cylinder and 5.51 kN for the square), versus the Kresling tubes which exhibit smaller peak forces for each unit cell (between 1.5 kN and 2.2 kN). Note each graph has a different scale. For protection of people or cargo, the multiple smaller peaks deliver a smoother and safer experience.
Overcoming manufacturing challenges
While O’Neil’s research affirms the compression advantages of Kresling origami tubes, a key challenge in implementing origami principles in engineering has been the manufacturing process. Structural materials can be difficult to fold and shape into complex origami geometries. Some materials cannot be folded at all without incurring damage. Many proposed methods for fabricating origami from structural materials can be difficult to automate and may even necessitate mechanical connections for forming a tube’s geometry.
These manufacturing hurdles make it difficult for companies to consider origami for the purposes of impact mitigation. However, O'Neil is proposing a solution. Filament winding, a manufacturing process commonly used in the industry to efficiently produce composite cylindrical tubes, can break the manufacturing barrier. This approach merges the advantages of origami with those of carbon fiber reinforced epoxy resin materials, offering weight-saving benefits compared to metals due to their superior strength and stiffness-to-weight ratio.
“Jimmy's research work on composite origami tubes is highly impactful, since it can resolve two of the major problems of current composite technology: manufacturability and crashworthiness. The technology developed can be applied to aerospace, automotive, biomechanical to sports equipment.”
"It is fascinating to me that we can take this totally out-of-the-box approach of using a very particular pattern of creases and folds to solve engineering applications," O'Neil says. “The intricate geometric parameters of origami present a challenge, allowing researchers to fine-tune and optimize the desired response.”
While O’Neil’s manufacturing process in the lab currently requires significant effort, with each tube representing about 12 hours of work, the introduction of filament winding machines will significantly enhance efficiency, making it a viable option for industry applications.
The benefits to safety
O'Neil's research on impact mitigation with origami holds great promise for improving safety in various fields, where there is the potential for impacts higher than what a traditional linear spring could absorb. This includes any kind of vehicle, including for rocket landings. By exploring the potential of creases and folds, his work opens up new possibilities for creating structures that can absorb and mitigate energy during impacts.
Professor Salviato breaks down the complexity and importance of this research, "Impact-absorbing structures play a key role in increasing survival chances of passengers during a crash. The use of composites has the potential to lead to significant weight savings while also increasing the amount of energy absorbed during the crash compared to traditional metallic crash absorbers. However, obtaining a controlled energy absorption with composites can be extremely challenging. Jimmy's approach of using origami architecture to enhance and better control energy dissipation in composite structures can be a game changer"
O'Neil muses, "Origami is like a puzzle. What parameters can I tweak and change to get the optimized response I want? It takes a lot of work, but it's really fun to do." With his innovative approach and determination, O'Neil is pushing the boundaries of engineering, paving the way for safer and more efficient structures through the adaptation of an ancient art.
Go to the source
Energy absorption behavior of filament wound CFRP origami tubes pre-folded in Kresling pattern. James O’Neil, Marco Salviato, Jinkyu Yang, Composite Structures, Volume 304, Part 2, 2023.